第3回:歴史から学ぶ「エバポレータ」の小型/軽量化技術開発のお話
2021.11.10
元デンソー認定プロフェッショナル
夢双造研究所 大原敏夫
(㈱最上インクス 技術アドバイザー)
今回は、当記事にてご紹介する3種類の写真の中(写真1)より「一番左にあるエバポレータ」の当時を振り返りながら小型/軽量化技術開発のご紹介をさせていただきます。
図1は40年前(1980年代当時)の代表的な「3種類のエバポレータ構造」を示しております。左から「フィン&チューブ型」「サーペンタイン型」「プレート積層型」と言います。以下に3種類の構造を簡単に説明いたします。
■「フィン&チューブ型」
チューブを通し、拡管にて機械的にフィンと固定する構造です。
■「サーペンタイン型」
押し出しの偏平チューブを蛇行状に曲げて、間にコルゲートフィンを挟んでロウ付けする構造です。
■「プレート積層型」
タンク機能を有する部位を持った薄板金属プレートを製作し、そのプレート間にコルゲートフィンを挟んでロウ付けする構造です。
当時「プレート積層型」は主に米国の自動車メーカーで多く使用されており、これを詳しく調べた結果「プレート積層型」が非常に性能的、かつ小型/軽量化においても大変優れた構造になっていることが分かりました。優れていた具体的内容としては、
1)フィン高さを圧倒的に小さくできるため集積度(小型化)が増します。
2)チューブを並列に並べているので、並行流にすることで冷媒の圧力損失を圧倒的に低減できます。
これと比べ日本の自動車メーカーで使用していた「サーペンタイン型」には性能及び小型/軽量化において米国に劣勢な状況でした。具体的な課題は、
1)一本の偏平押し出し管を蛇行状に曲げている構造であり、冷媒管路が長く、結果として当然冷媒圧力損失は多大になります。
2)偏平管の曲げ幅等の限界から菅の間隔は狭められず、集積度(小型化)も増すことが出来ません。
この様な状況のままでは、日本の自動車熱交換器は米国に劣勢から変わらないという危機感の中で、日本の熱交換器メーカーも「プレート積層型」に切り替えて行く方向になりました。しかし技術開発を進めて行く中で、米国の「プレート積層型」にも小型/軽量化に欠点があると突き止めることが出来ました。具体的には「冷媒の集合/分配機能を持つタンクがあまりにも大きいということ」です。しかも「上下に二つもある構造」になっており、更なる小型/軽量化には課題があるとの考えのもとに、これを凌駕できれば米国を超える「新型エバポレータ」を作れるという想いから「片方だけに冷媒の集合分配タンクを持つ」日本独自構造の「シングルタンク式(図2)」の開発に成功し、日本で先行したのち世界で主流の高性能、かつ小型/軽量化を実現した「新エバポレータ」になっていきました。
次回コラムでは、より具体的な小型/軽量化の手法をご紹介させていただきます。
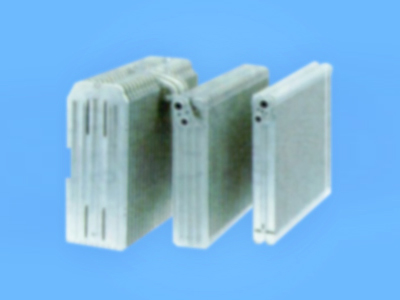
2019年名古屋銀行「次世代自動車セミナー」講演資料
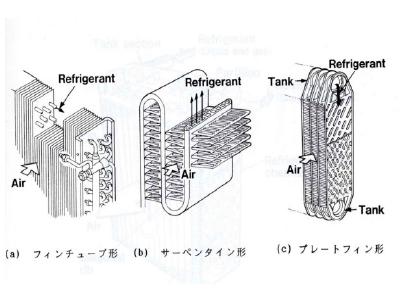
1988年SAE Parer 880047
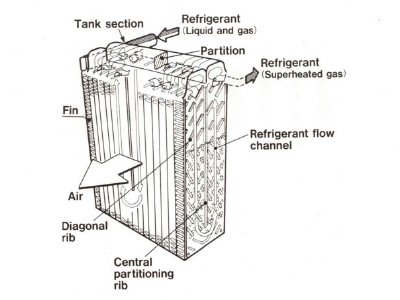
日本冷凍協会論文集
「カーエアコン用高性能エバポレータの開発」1989-7